Michelin développe ses pneus sur simulateur
De la course à la mobilité, le manufacturier français développe désormais tous ses pneus sur simulateur. Une avancée technologique, économique et écologique.

La coque carbone montée sur 6 vérins tressaute face à un immense écran. Dans le cockpit, le pilote Felipe Albuquerque enchaîne les tours de circuit de Spa Francorchamps au volant de son Hypercar. Derrière la vitre une batterie d'écran, de puissants logiciels nourris de data et une poignée de techniciens qui surveille avec attention l'évolution du pilote en enregistrant la moindre de ses données.
Bienvenue chez AOTech, le centre d'essai virtuel avec lequel Michelin développe ses pneumatiques. Un centre unique, le seul au monde homologué par l'organisateur des 24 Heures du Mans, l'ACO (Automobile Club de l'Ouest) où tout pilote (quels que soient son niveau et sa renommée) doit passer avant de pouvoir rouler le sur la piste sarthoise.
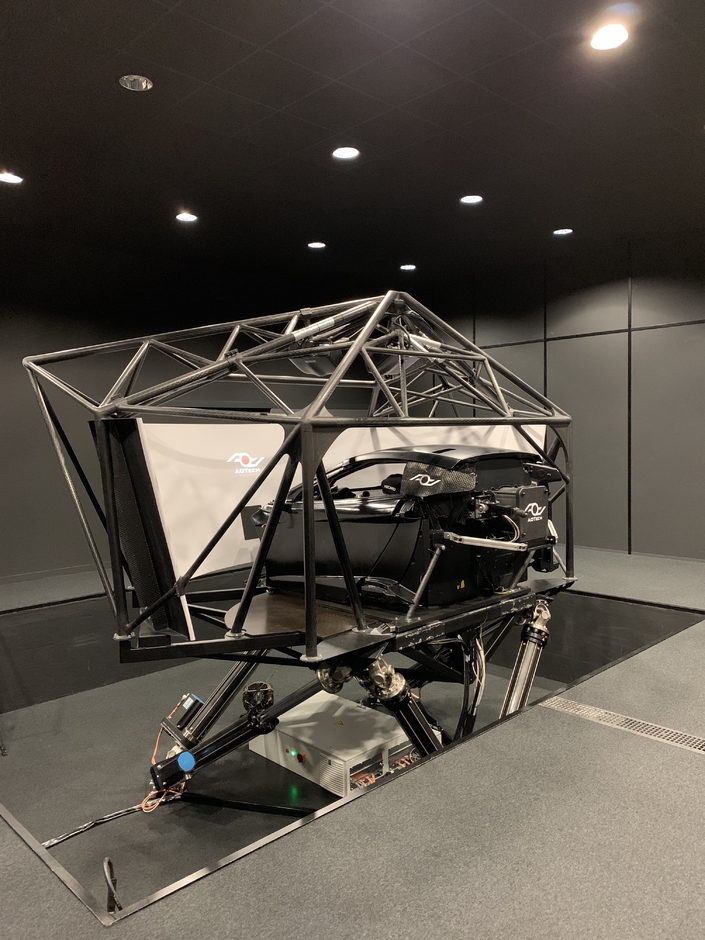
Une manière de s'assurer en amont de la course que les pilotes maîtrisent bien les conditions de course, connaissent la réglementation, respectent les consignes, etc. Une sorte de pré-test obligatoire avant la piste, histoire d'éviter au maximum les risques en course. Et c'est aussi avec ce simulateur que Michelin développe de façon « virtuelle » les pneumatiques qui équipent les 16 Hypercars du plateau 2023 du Mans. Et ce n'est pas un hasard !
Le sport lab
« La compétition est un formidable terrain de jeu, c'est un laboratoire, une porte d'entrée technologique sans contrainte de production industrielle. Avec les 16 véhicules qui nous équipons au Mans se sont plus de 100 000 km de DATA qui nous sont remontées en une seule course. Quand on fait des tests d'usure de pneu en ville, il nous faut plusieurs mois d'essais » explique, Mathieu Bonardel, responsable Michelin Motorsport. « On est capable de comprendre en direct, en temps réel, l'interaction de la voiture en piste avec la vie du pneu ».
Ce qui permet de réaliser des tests et la conception de pneumatiques sans avoir de présence physique sur le terrain. Un gain de temps et d'argent, mais pas que, comme l'explique le pilote Felipe Albuquerque, « lorsque l'on va réaliser des tests sur un circuit et que les conditions de piste ou la météo ne sont pas favorables, on ne roule pas, c'est beaucoup d'énergie et de stress pour rien, alors que là, on est sûr de pouvoir travailler ».

Et d'insister sur le fait que le simulateur ne retranscrit pas toujours très finement les conditions de course. « Sur le simulateur le grip est par exemple constant sur l'ensemble du circuit choisi ce qui n'est pas le cas dans la réalité. La course n'est pas uniquement une somme d'équations qui misent bout à bout permettent de gagner. »
Il n'empêche ! Si le simulateur peut encore être perfectible (peut bientôt s'enrichir d'Intelligence Artificielle), il permet de reproduire la réalité dynamique à travers l'interaction de trois modèles numériques : un premier reproduit fidèlement le profil et l'adhérence du circuit, un deuxième (qui représente le châssis ou la voiture entière) et un dernier pour simuler dans les moindres détails le comportement des pneumatiques. Au volant du simulateur, le pilote teste les différents types de pneus dans toutes les configurations possibles. Au final, le ressenti subjectif du pilote est croisé avec les mesures objectives du simulateur pour compléter les analyses.
Résultat : « On divise par deux le temps de développement et par trois le nombre de pneus utilisés, car ceux qui sortent sont d'une bien meilleure qualité, donc on gaspille moins » résume Mathieu Bonardel. Pour l'édition du centenaire du Mans cette année, le manufacturier a pu ainsi développer à partir de simples données techniques (data) en 10 mois des trains de pneus pour des voitures qui n'existaient pas encore. Le simulateur est une porte ouverte, une anticipation sur l'avenir. Et ce qui vaut pour la compétition, vaut également pour la voiture au quotidien.
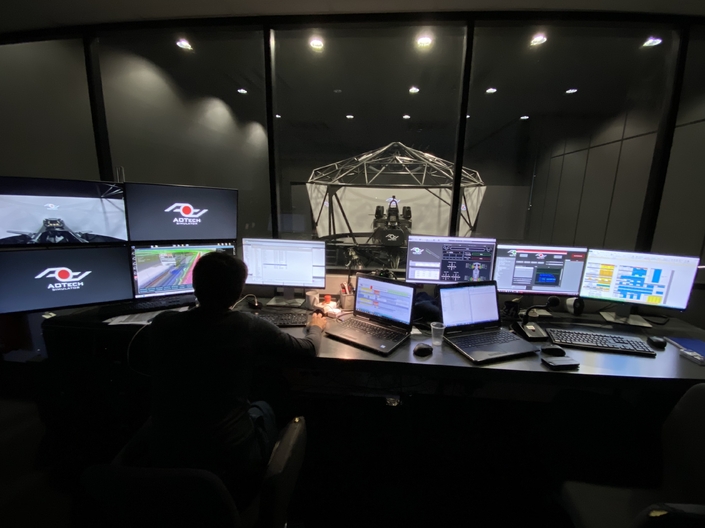
De la piste à la route
Avec le développement de l'électrification des véhicules et leurs nouvelles utilisations (modèle autonome, voiture partagée…) et dans un souci de moindre impact sur l'environnement « le pneu le plus durable est celui qui utilise le moins de matière et se conserve plus longtemps », une lapalissade prise comme ligne de développement chez Michelin.
Sur un pneu de série la principale source de production de CO2, c'est la résistance au roulement, cela équivaut à l'équivalent d'un plein sur cinq pour les voitures thermiques et sur une voiture électrique à 50 km d'autonomie de la batterie. Une paille compte tenu du temps de recharge de la batterie et de l'autonomie globale de celle-ci.
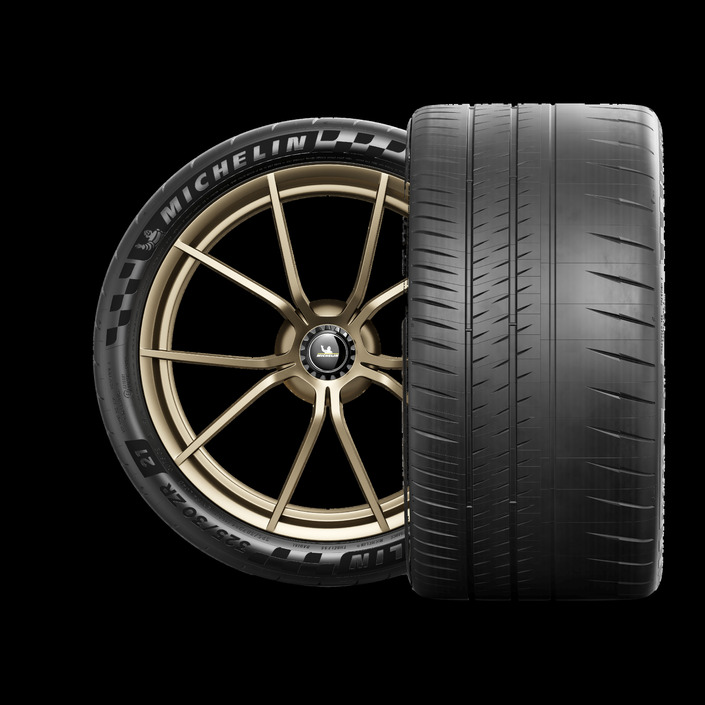
Pour Bruno de Feraudy, Directeur des activités première monte Michelin, « les attentes des constructeurs et des clients ne sont pas les mêmes. » L'électrification du marché automobile entraîne de nouvelles contraintes dans la conception des pneus. Il faut comme, comme pour la compétition, repartir d'une feuille blanche, avec des nouveaux véhicules aux profils inédits, sans que le conducteur ne perde les sensations et les qualités intrinsèques promises par le constructeur. « Sauf, qu'entre les problèmes environnementaux et les attentes des conducteurs, il y a des antagonismes, pour ne pas dire du non-sens écologique. On veut des voitures mieux équipées, dotées de batteries performantes pour rouler plus longtemps, résultat, on obtient des véhicules plus lourds, donc plus énergivores sur lesquels les pneumatiques une durée de vie en moyenne inférieure de 20 à 40 % par rapport au modèle thermique » souligne Bruno de Feraudy.
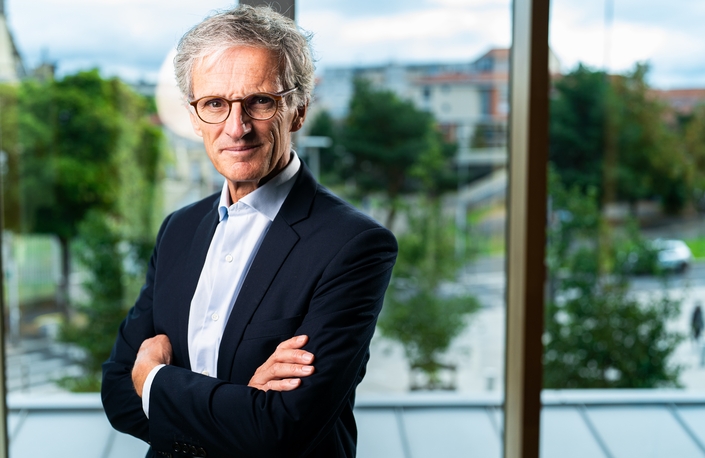
Sans parler des autres contraintes comme celle liée au bruit. Avec l'électrique, « 70 % du bruit provient du roulement du pneu sur le bitume ». Là encore, il convient de trouver une solution pour réduire cette sonorité parasite que le conducteur ne supporte plus.
Le tout, en un minimum de temps pour ne pas entraver le développement du marché, notamment en Chine, où 80 % des voitures neuves vendues sont électriques. La réponse passe pour Michelin par la simulation et le virtuel. À terme, le manufacturier y voit une arme absolue de « compétitivité ». C'est comme cela qu'a été développé le High Load Capacicty Tyre qui permet au pneu une surcharge de 300 kg à diamètre constant ; c'est aussi ce type de développement et de conception qui a permis de mettre une mousse réductrice de bruit dans les pneus pour véhicules électriques.
Temps, argent, environnement
Pour Romain Bouchet, chef du programme simulation, « l'aide virtuelle permet aux constructeurs de baisser le coût de développement en ayant un résultat cohérent ». Le but du travail par simulation et de ne plus avoir de prototype et de sortir un pneu efficient directement et de réduire voire de supprimer les nombreuses phases de tests sur pistes.
Avec Canopy Simulation, leader mondial de la simulation de « temps au tour ». Les logiciels de simulation combinent les modèles circuit, voiture et pneumatiques avec un simulateur de trajectoire très avancé qui reproduit le comportement d'un « pilote virtuel idéal ».
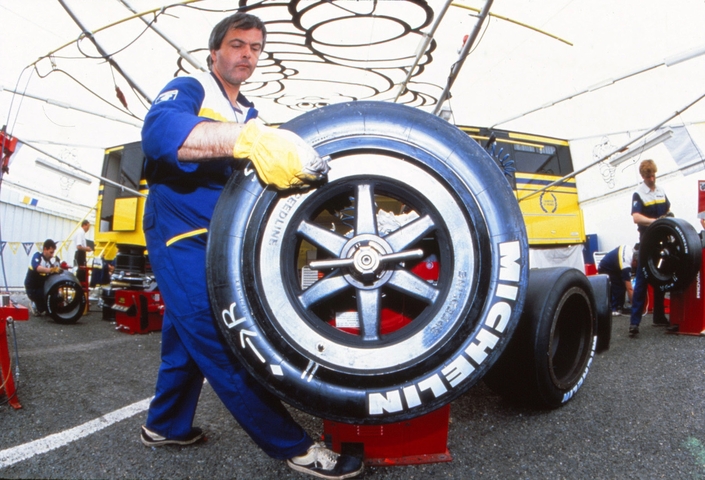
En motorsport, le pilote virtuel réalise les tâches les plus standardisées. Il simulera par exemple les 4 heures de conduite nécessaires pour compléter 4 relais au Mans et évaluer la constance des pneus. Sur la route, il permet aux constructeurs automobiles de reproduire différentes configurations conducteurs, d'utilisation de la voiture et des pneus associés.
Toutes les déformations et contraintes du pneu sont modélisées puis encapsulées et mises dans le simulateur afin de comprendre les particularités des différentes composantes du pneu et leurs interactions.
Encore faut-il « abreuver » le logiciel avec les bonnes données. « Aujourd'hui, le simulateur ne sait pas les effets d'un nouveau matériau dont il ne connaît pas les contraintes techniques et physiques, il faut lui apprendre à partir de la data, du terrain, précise Mathieu Bonardel.
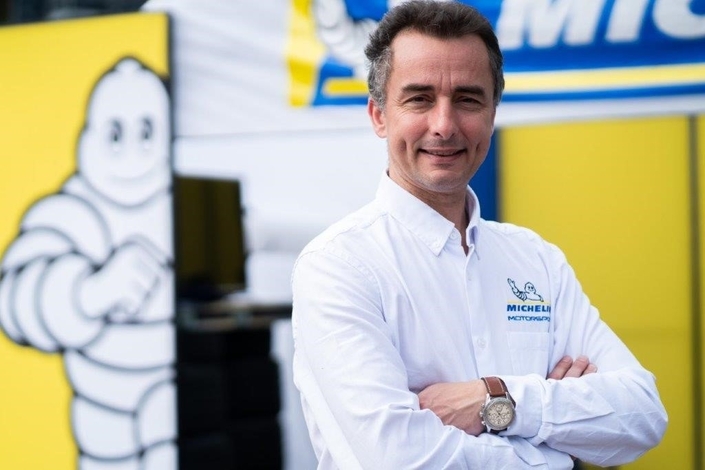
Sur le plan du développement de pneus plus durables par exemple « En 2030 nous serons sur des pneus de série composés à 40 % de matières premières biosourcées, régénérées et recyclées, comme de la silice à base d'écorce de riz, de bouteilles de plastiques recyclées pour le cordage textile, de pots de yaourts pour la bande de roulement contre 20 % actuellement », cela ne peut se faire qu'avec le simulateur. L'humain conserve néanmoins le dernier mot, pour valider le résultat virtuel. À moins que l'intelligence artificielle ne vienne s'y substituer un jour peut-être.
Déposer un commentaire
Alerte de modération
Alerte de modération